From Design to Manufacturing
With more than 4,000 active licenses, KISSsoft is known as a global market leader in the field of gear and transmission design software. With its modules and functionalities related to gear manufacturing and inspection, KISSsoft delivers powerful analysis tools for production, supporting the close collaboration and data exchange between design, manufacturing and quality control.
Assisting Tool Design
No matter if tools with protuberance, semi-topping or even with a modified pressure angle are required, KISSsoft assists the design of cutting tools in various ways: Tools can be selected from an existing database or specifically designed for highest gear contact ratio, maximum gear root radius and many more. If a new tool is required, the data can be sent directly to the tool manufacturer.
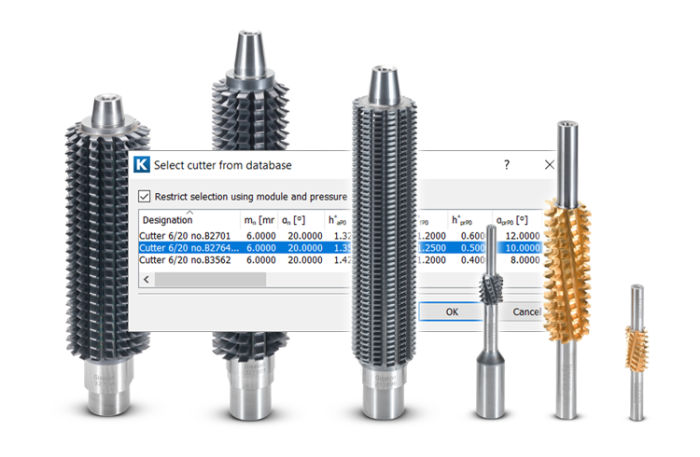
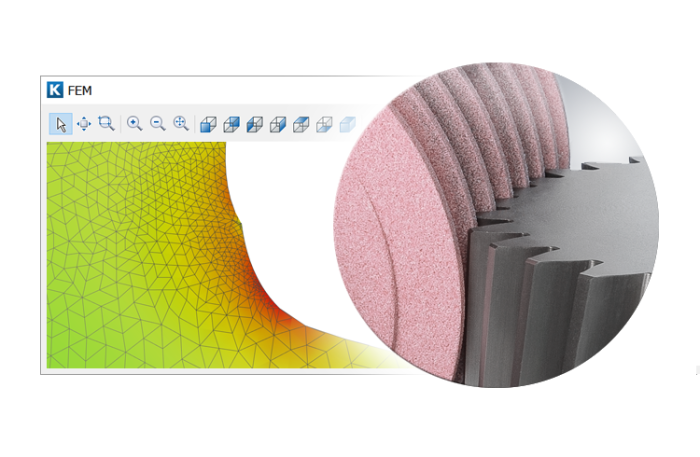
Threaded Wheel Grinding
Both grinding processes, profile and threaded wheel grinding, are simulated in KISSsoft. At the click of a button, the grinding tool addendum can be calculated for different grinding depth. To rate the stress concentration introduced through a grinding notch, the 2D FEM and 3D FEM methods are available.
Dressing Disc Verification
KISSsoft checks whether an existing dressing disc can be used, reducing tool cost and lead time. The resulting gear modifications such as tip relief or pressure angle modifications are calculated from the tool geometry and are displayed in a profile diagram, including tolerances. These can be compared with the initially designed modifications and assessed for noise excitation.
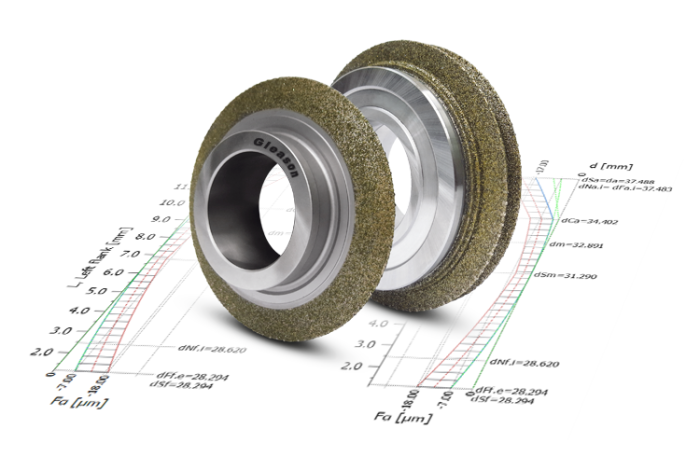
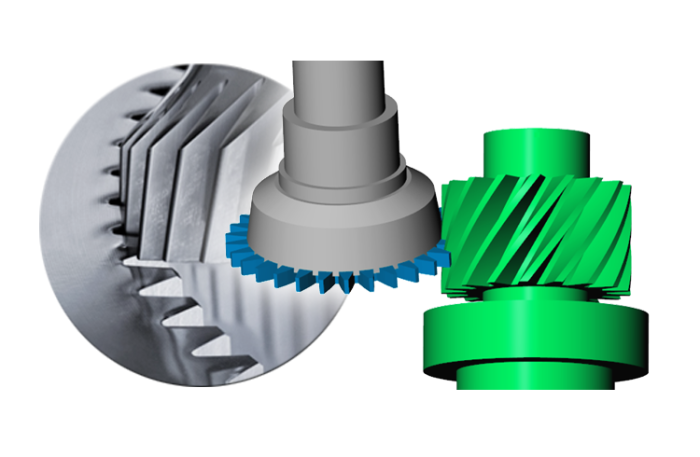
Collision Check
KISSsoft analyzes the possibility of the tool colliding with the workpiece, on the basis of the cross-axis angle and tool diameter, shaft contour or internal shaft diameter. For a detailed analysis, the verification for a potential collision by Gleason is recommended.
Gear Inspection
For gear inspection, the nominal measurement grid data can be calculated and exported from KISSsoft. The measured flank topography is imported into KISSsoft, analyzing its load behavior and noise excitation using the contact analysis. This process allows to verify manufactured gears and to ensure the required quality of the transmissions.
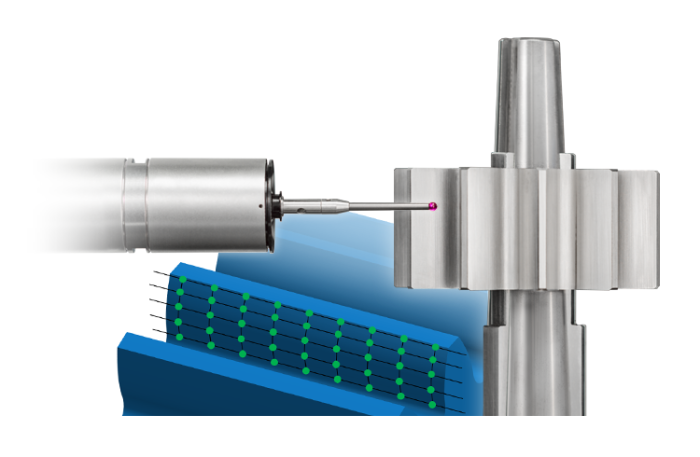
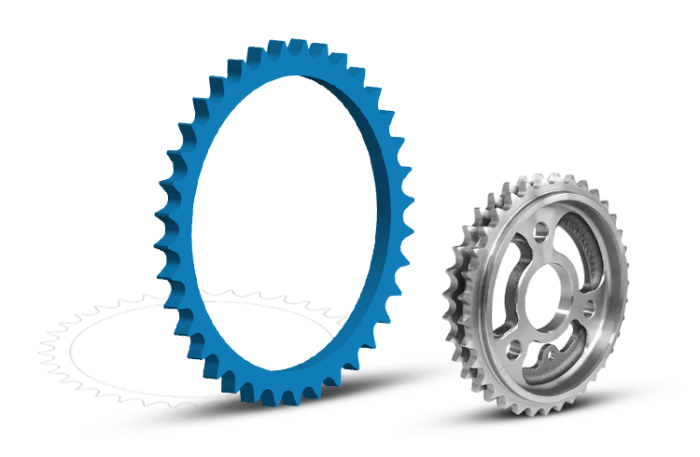
Non-Involute Gears
For non-involute gears, KISSsoft verifies the feasibility using generating cutting processes and calculates the tool reference profile or specific tool form. Typical applications are straight flank, cycloid or sprocket gears, used in park locks or sprockets for chain drives. The hob profile is calculated from the tooth form and provided as 2D DXF export.